MAXIMIZE EFFICIENCY IN NARROW AISLES
In modern logistics, narrow aisle warehouses provide a strategic advantage by maximizing vertical storage and optimizing space.
While they offer exceptional storage density, selecting the right equipment is crucial to effectively navigate the challenges of these compact environments.
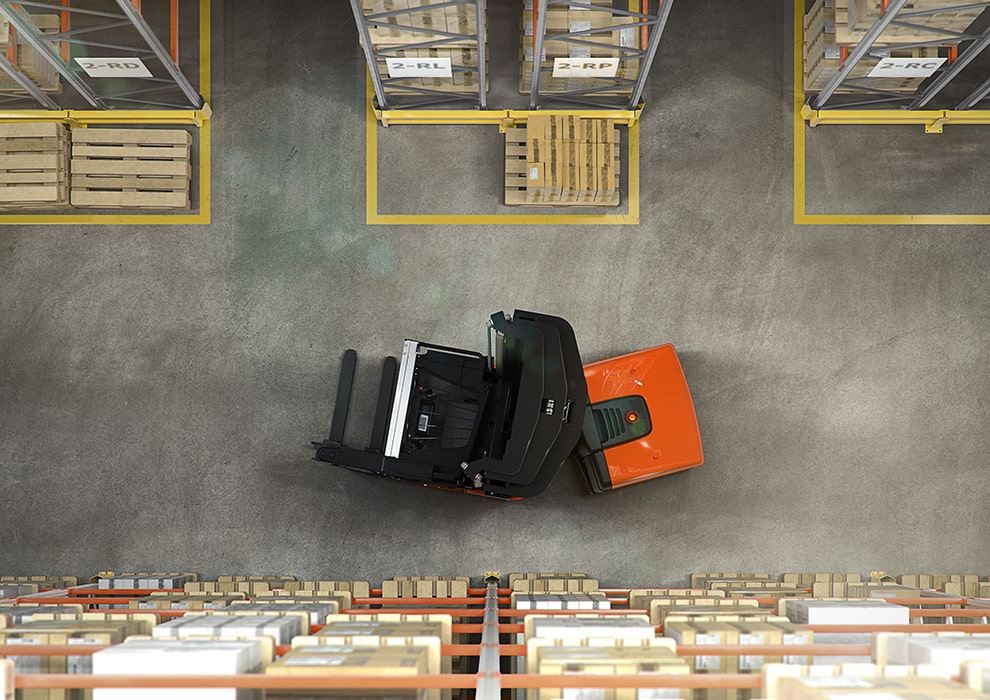
The ups and downs in narrow aisles
Narrow aisle warehouses offer a unique advantage in maximizing storage density by significantly increasing the amount of racking within a given footprint. Businesses can store more inventory without requiring additional square footage by optimizing vertical space with taller racks.
This high-density layout is particularly beneficial for operations with large volumes of goods, as it allows for more efficient inventory management and often integrates seamlessly with modern warehouse management systems. However, this efficiency comes at a cost. Narrow aisle designs necessitate specialized equipment, as standard forklifts are too large to maneuver in these tight spaces. The initial investment in infrastructure and machinery can be high, and operations may become more complex, requiring precise equipment and trained operators to navigate the limited aisle widths effectively.
Despite these challenges, the space-saving and operational benefits often outweigh the difficulties, making narrow aisle warehouses popular for businesses aiming to optimize their storage capabilities.
EQUIPMENT TYPES FOR NARROW AISLE OPERATIONS
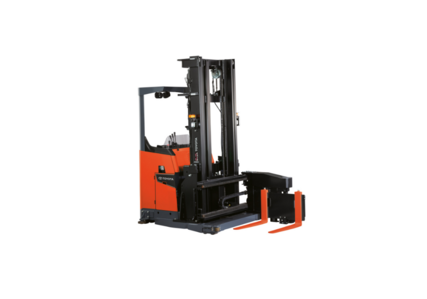
SWING REACH
Swing reach trucks are designed with a pivoting fork carriage mounted on a fixed mast. The fork carriage can swing up to 90 degrees left or right, allowing operators to access loads on either side of the aisle without repositioning the truck itself.
The operator typically remains at ground level, and the truck excels in moderately high stacking applications.
Benefits
- Efficient in moderately narrow aisles.
- Simple operation with lower operator training requirements.
- Cost-effective compared to turret trucks.
Challenges
- Limited vertical reach compared to turret trucks.
- Fork movement is less versatile, restricting handling precision at extreme heights.
- Requires slightly wider aisles than turret trucks.

TURRET TRUCK
Turret trucks feature a rotating turret mechanism on the mast, allowing the forks to rotate a full 180 degrees. This capability enables the truck to pick up or place loads on either side of the aisle without turning.
Additionally, the operator is often elevated with the turret, offering better visibility and control at high stacking levels.
Benefits
- Operates efficiently in very narrow aisles (VNA).
- Ideal for high-density, high-level storage.
- Superior precision in pallet handling at extreme heights.
Challenges
- Higher upfront and maintenance costs.
- Requires specialized training for operators.
- Limited versatility outside of narrow aisle environments.
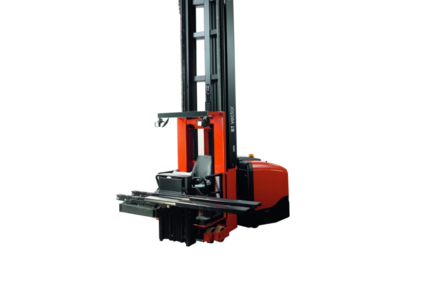
SHUTTLE FORKS
Shuttle fork machines feature a fork carriage that can shift left or right, enabling lateral pallet handling without moving the truck itself. This side-to-side movement allows the operator to place or retrieve pallets on either side of the aisle while keeping the truck in a fixed position. Shuttle forks can be fitted to both man-up and man-down VNA trucks to maximize efficiency in high-density racking systems.
Benefits
- Efficient pallet handling in very narrow aisles (VNA).
- Reduces the need for mast rotation or truck repositioning.
- Enhances productivity by enabling side-to-side pallet access.
Challenges
- Adds complexity and weight to the mast.
- Slower than turret systems for deep stacking.
- Requires precise alignment and skilled operation for accuracy.
OPERATOR POSITIONS
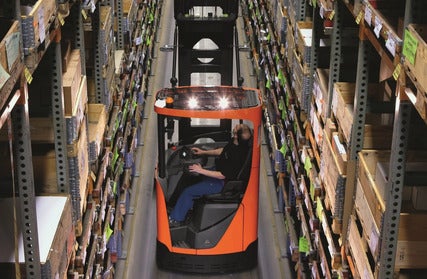
MAN DOWN
Man-down VNA trucks keep the operator at ground level while only the mast and forks are raised to access pallets at height. These trucks usually feature rotating or shifting fork systems—such as turret or shuttle forks—to handle pallets without the need to turn or reposition the truck in the aisle. Man-down configurations are primarily used for full-pallet handling in very narrow aisle environments, where high throughput is a priority.
PROS AND CONS
Among the benefits of man-down trucks are their simpler design, lower overall cost, and faster travel speeds when compared to man-up machines. They are well-suited for efficient pallet handling in high-density storage systems. However, they do have limitations.
Because the operator remains on the ground, visibility at high levels is restricted, making the truck reliant on camera or sensor systems for accurate placement. In addition, order picking and manual inspection is not possible with man-down trucks, which limits their flexibility in certain warehouse operations.
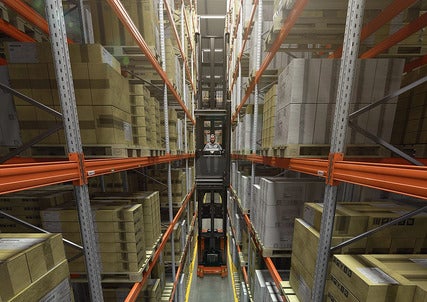
MAN UP
Man-up VNA trucks lift both the operator and the forks together, allowing the driver to be at the same height as the pallet during storage and retrieval. This provides excellent visibility and precise control, especially at high lift heights, making man-up trucks ideal for applications where accuracy is critical. They are commonly used for full-pallet handling and order picking in high-density warehouse environments with very narrow aisles.
PROS AND CONS
The main benefits of man-up trucks include superior visibility at height, enhanced control during pallet handling, and the ability to perform both full-pallet storage and order-picking operations.
While these advantages are significant, the elevated operator position places added emphasis on safety systems and specialized training. Prioritizing stability often means operating at reduced travel speeds and involves a slightly higher investment in purchase and maintenance.
Flat Floors – A Must for Narrow Aisles
Flat floors play a crucial role in unlocking the full potential of very narrow aisle (VNA) systems. Because VNA trucks operate with tight clearances and lift to extreme heights, the quality of the warehouse floor directly affects how safely and efficiently they can perform. A level, smooth floor ensures that trucks remain stable, loads stay secure, and operators can work with confidence—even at the highest racking levels.
In man-up trucks, where the operator is elevated with the load, any floor imperfections can be felt more strongly, leading to slower performance and increased fatigue. In both man-up and man-down machines, uneven flooring can interfere with guidance systems and reduce handling precision. Over time, it also contributes to unnecessary wear on components like wheels, masts, and electronics—leading to more frequent service, higher parts costs, and avoidable downtime.
Investing in a flat floor is not just about meeting a technical requirement—it’s about protecting your investment in a high-performance storage system. When done right, it enables maximum productivity, lower maintenance costs, and long-term reliability. For warehouses looking to optimize space, increase throughput, and stay competitive, VNA is a powerful solution—and a well-prepared floor is the first step toward making it a success.
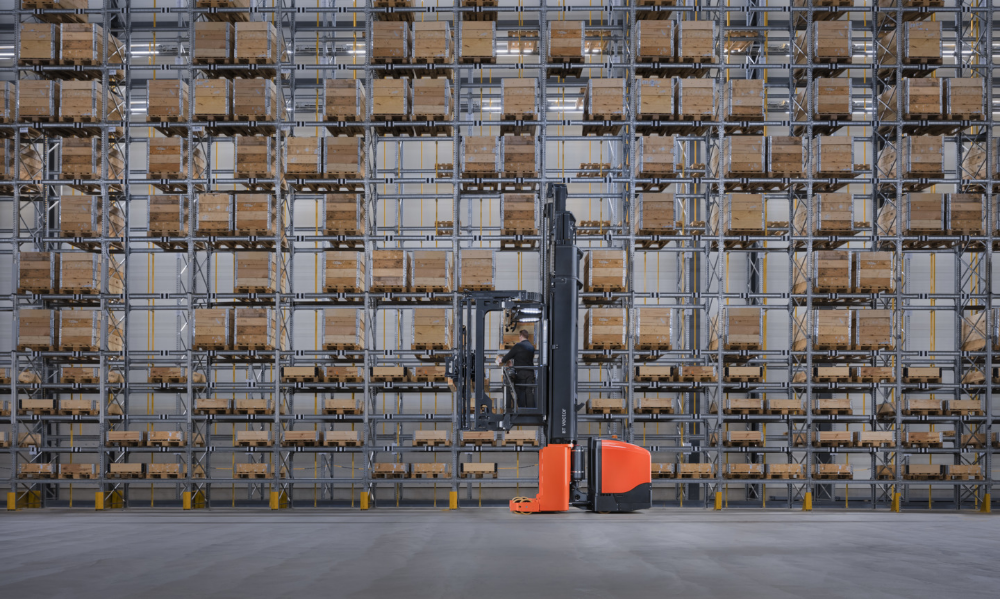
SIMILAR TO VNA MACHINERY
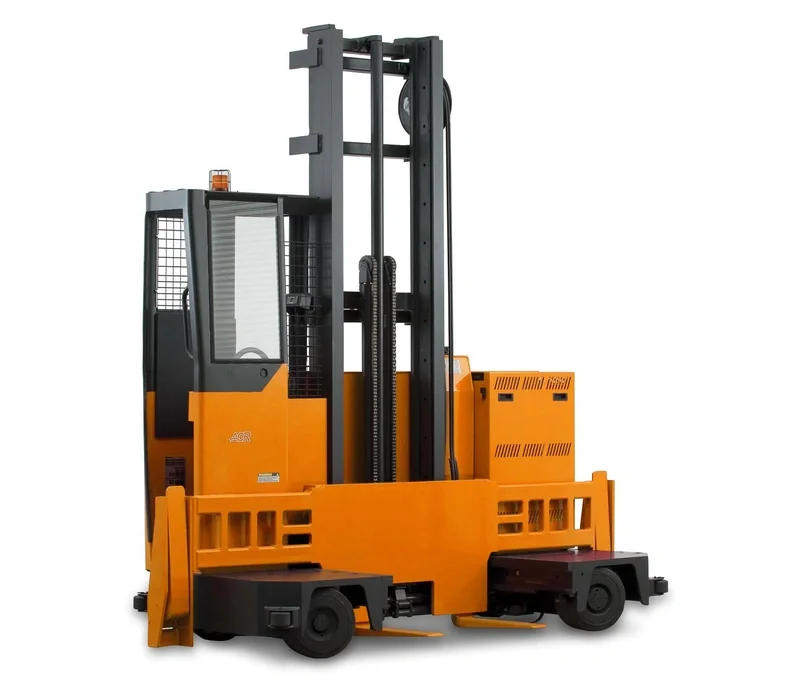
Side loaders - for long and oversized loads
Sideloaders are unique in that they are designed to lift and carry loads parallel to the truck’s body. The forks and mast extend sideways, making them ideal for handling long or bulky items such as pipes, lumber, or metal sheets in narrow aisles. The lateral design gives operators excellent visibility when placing loads on racks.
Benefits
- Excellent for long, oversized, or awkwardly shaped loads.
- Versatile for both narrow aisle and open space use.
- Provides stable load handling due to its side-mounted design.
Challenges
- Less effective for standard palletized goods.
- Requires additional operator skill for precise load placement.
- May not utilize vertical storage as efficiently as turret trucks.